Wirtgen Group filter types
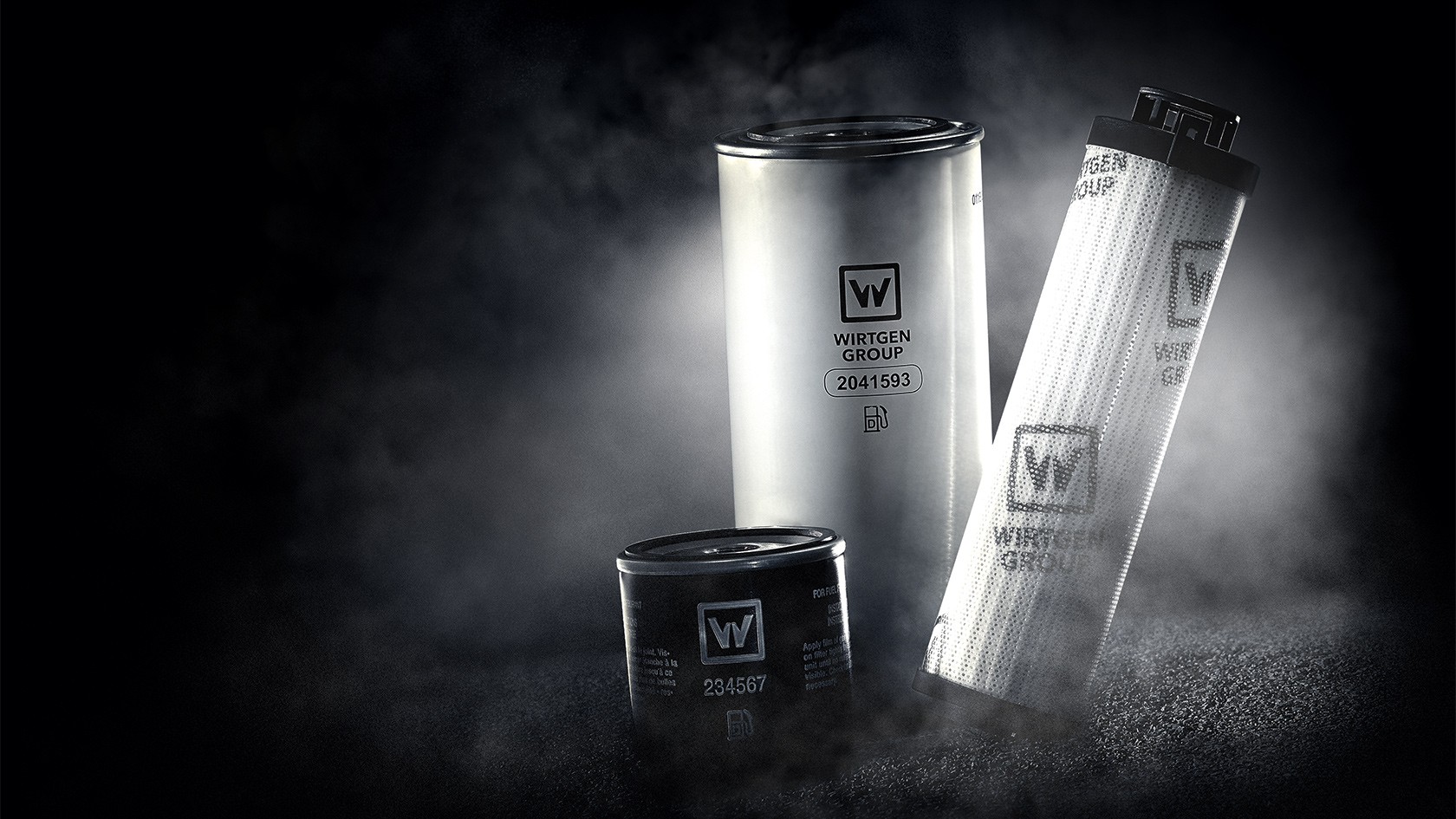
The reliability of combustion engines depends on a supply of clean air, oil, and fuel. There are three separate systems for providing these three essentials, each of which needs its own filter system.
Air filters clean the air required for combustion and thereby minimise the risk of damage to engine components. To prevent damage, all filters only allow dirt particles up to a certain particle size in the micrometre (µm) range to pass through it. The exact particle size depends on the engine. As a rule, WIRTGEN GROUP machines are fitted with upstream pre-filters that reduce the load on the actual air filter.
The amount of air required by the engine is a decisive factor when choosing the right pre-filter. Two different upstream system options are presented here, both of which serve the same purpose within the system. Air pre-filters with an impeller and cyclone air pre-filters.
A rotor (impeller) is driven by the intake air drawn into the combustion engine. The high speed of the impeller subjects dirt particles to very high centrifugal forces and, as a result, even the smallest particles are ejected through a dust discharge valve in the housing.