KLEEMANN cone crushers
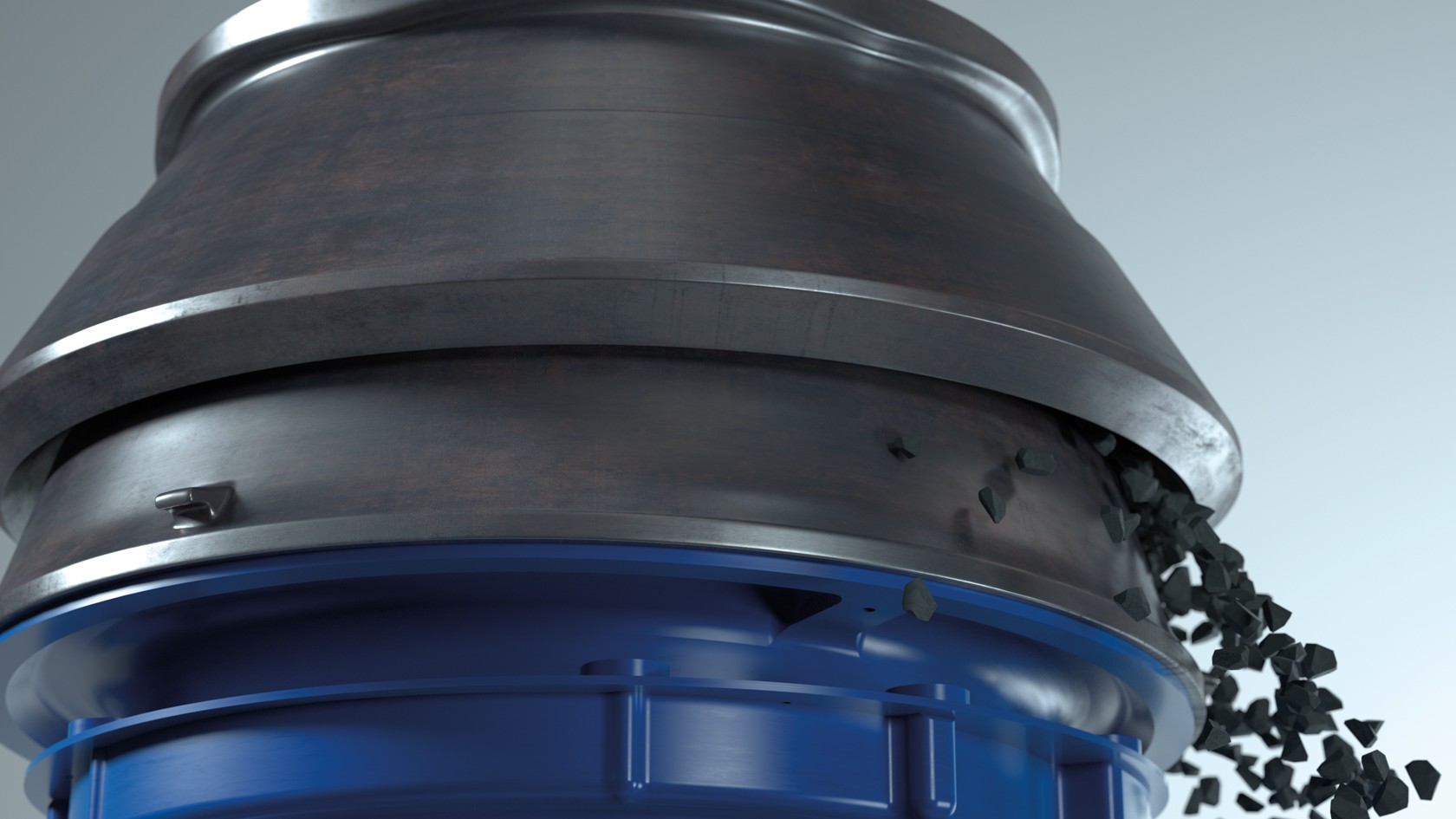
Cone crushers are the ideal choice for use in medium-hard to hard and abrasive natural stone and for processing raw materials in mining applications. The cone crushers deliver standardised final cubic grain sizes in the second and third crushing stages. The cone crushers are available in various sizes and configurations and for a variety of applications.
The KX series* cone crushers are typically used as secondary and tertiary crushers. In this case, the material entering the crusher is crushed between the rigid crushing shell and the moving crushing cone. The rotating eccentric around the main shaft is driven by the countershaft. The rotation causes the head to wobble, which alternately opens and closes the crushing gap.
Adjustment of the gap setting (Open Side Setting OSS = feed opening / Closed Side Setting CSS = closed crushing gap) enables variation of the final output grain size.
* The KX series includes the following models:
Principle
Cone crushers crush the feed material in a circulating, alternately opening and closing crushing gap between the bowl liner and the crusher cone by pressure crushing. Opening and closing also takes place simultaneously on the opposing sides of the crushing chamber.
Cone crushers are available in a variety of designs. In the case of the cone crushers used by KLEEMANN, the crusher shaft is press-fitted into the main frame. The mantle carrier is mounted on an eccentric drive unit. The rotation of the drive unit alternately opens and closes the gap between the mantle and the bowl liner. The grain size to be produced is altered by raising or lowering the bowl liner.
Cone and gyratory crushers are predominantly used when impact crushing is no longer possible due to the high compressive strength of the crushed material, or when the costs of wear are not economically justifiable due to the abrasiveness of the feed material.
Due to their design, cone and gyratory crushers are limited with regard to the feed size and the achievable reduction ratios.
On mobile plants, cone crushers are used predominantly for post-crushing in the secondary and tertiary crushing stages.
Application | Identification markings |
Max. F.size in mm |
Closed side setting in mm (CSS) | Casting alloy | Version |
---|---|---|---|---|---|
Secondary crushing stage For final product >25 mm Reduction ratio* 3.5 to 5:1 Open cycle Feed opening width |
Notch on one side | 220-240 | 25-45 | MnCr 18.2 | S-CONE C.18 |
MnCr 20.3 | S-CONE C.20 | ||||
175-190 | 19-38 | MnCr 18.2 | S-CONE M.18 | ||
MnCr 20.3 | S-CONE M.20 | ||||
130-145 | 16-32 | MnCr 18.2 | S-CONE F.18 | ||
MnCr 20.3 | S-CONE F.20 | ||||
Tertiary / quaternary crushing stage For final product <25 mm Reduction ratio * 2.5 to 3:1 Closed cycle Long calibration zone |
Notch on two sides | 102-114 | 13-25 | MnCr 18.2 | SH-CONE C.18 |
MnCr 20.3 | SH-CONE C.20 | ||||
82-93 | 10-22 | MnCr 18.2 | SH-CONE M18 | ||
MnCr 20.3 | SH-CONE M.20 | ||||
52-62 | 10-19 | MnCr 18.2 | SH-CONE F.18 | ||
MnCr 20.3 | SH-CONE F.20 |
Application | Identification markings |
Max. F.size in mm |
Closed side setting in mm (CSS) | Casting alloy | Version |
---|---|---|---|---|---|
Secondary crushing stage For final product >25 mm Reduction ratio* 3.5 to 5:1 Open cycle Feed opening width |
Notch on one side | 116-131 | 16-32 | MnCr 18.2 | S-CONE F.18 |
MnCr 20.3 | S-CONE F.20 | ||||
138-157 | 19-38 | MnCr 18.2 | S-CONE M.18 | ||
MnCr 20.3 | S-CONE M.20 | ||||
179-199 | 25-45 | MnCr 18.2 | S-CONE C.18 | ||
MnCr 20.3 | S-CONE C.20 | ||||
Tertiary / quaternary crushing stage For final product <25 mm Reduction ratio * 2.5 to 3:1 Closed cycle Long calibration zone |
Notch on two sides | 71-80 | 10-19 | MnCr 18.2 | SH-CONE F.18 |
MnCr 20.3 | SH-CONE F.20 | ||||
99-111 | 10-22 | MnCr 18.2 | SH-CONE M.18 | ||
MnCr 20.3 | SH-CONE M.20 | ||||
130-142 | 13-25 | MnCr 18.2 | SH-CONE C.18 | ||
MnCr 20.3 | SH-CONE C.20 |
The right combination is what counts!
Mobile cone crushers should always be operated in the optimum range to ensure consistently high material output volumes in high final product quality from a cone crusher. In the case of KLEEMANN cone crushers, high process reliability is already assured when they leave the factory. Users can take advantage of application expertise from KLEEMANN to further optimize the crushing process. This starts with the selection and combination of the right tool, which consist of a crusher cone and a bowl liner.
The crushing tool tool-set for cone crushers contains everything you need for changing the crushing tools.
The crushing tool tool-set for cone crushers contains all the components you need for replacing the bowl liner, the mantle, the torch ring made from specially treated steel, the sealant and the materials required for their installation.
Once the tools are installed, they can no longer be distinguished from one another by shape or form. KLEEMANN therefore uses version-specific markings on the cones and bowl liners.
Standard
Short head