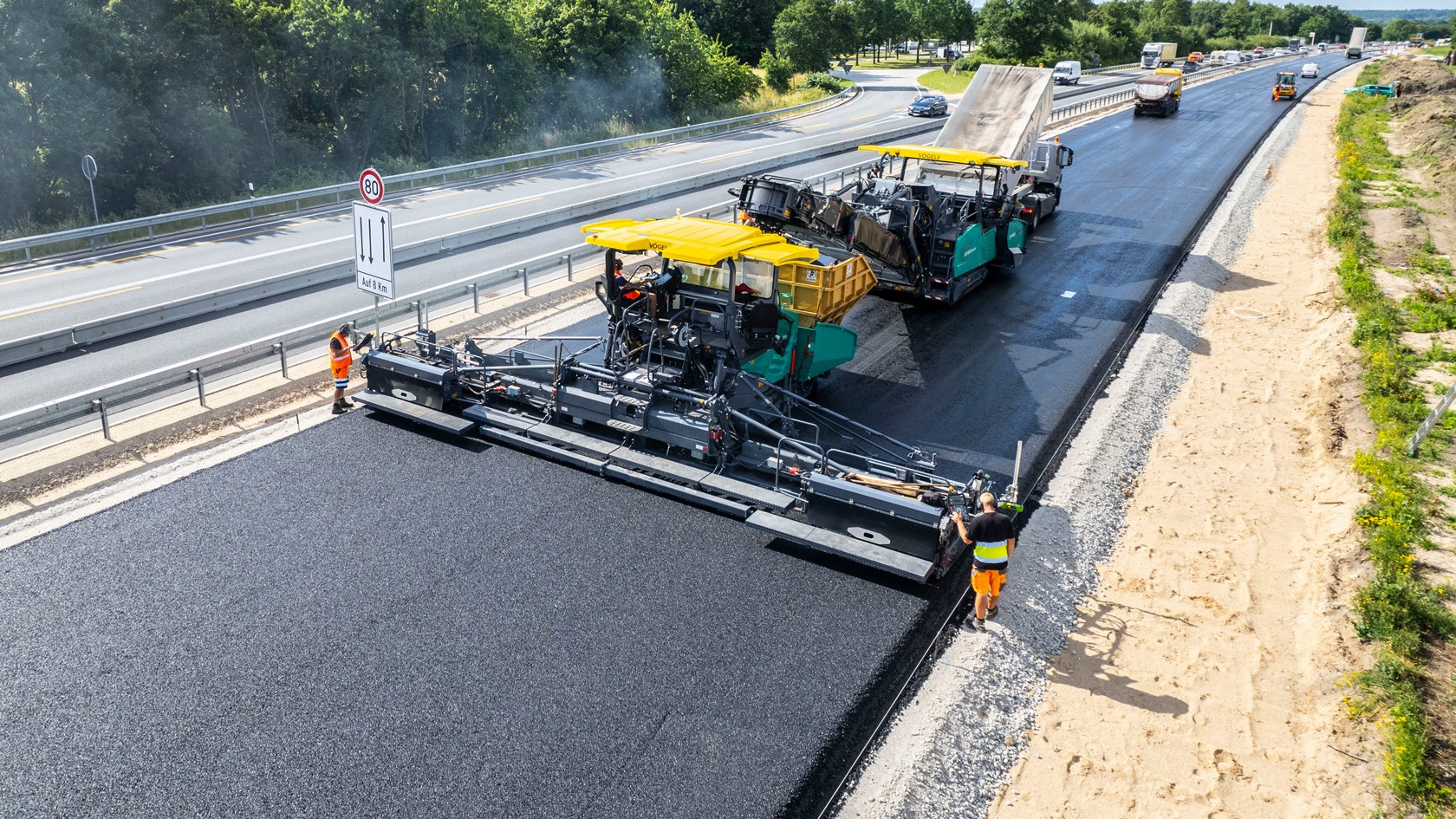
The aim of the screed's compacting systems is to achieve the greatest possible pre-compaction so that different layer thicknesses have less influence on the amount of rolling required for final compaction. VÖGELE employs the compacting systems listed below:
Applications
V and TV screeds can be used for all conventional mixes that are easier to compact. Less final compaction effort is necessary when TP1 and TP2 screeds are used. The two variants differ with regard to the compaction values that can be achieved; whereby all conventional mixes can be processed. The TP2 variant delivers a high level of pre-compaction, particularly in the case of thicker paved layers.
TVP2 screeds can be used for paving with all conventional mixes. This variant is also suitable for paving PCC (Paver Compacted Concrete), as surfaces paved using this method require no final compaction. The TP2 Plus variant offers even higher compaction values and is used in the VÖGELE InLine Pave train for the production of the binder course. Due to the immediately following paver, this layer must already have final compaction values. All compacting systems on VÖGELE screeds - tampers, vibrators and pressure bars - are independently controlled and can be switched on or off as required.
Compaction aggregates of extending screeds