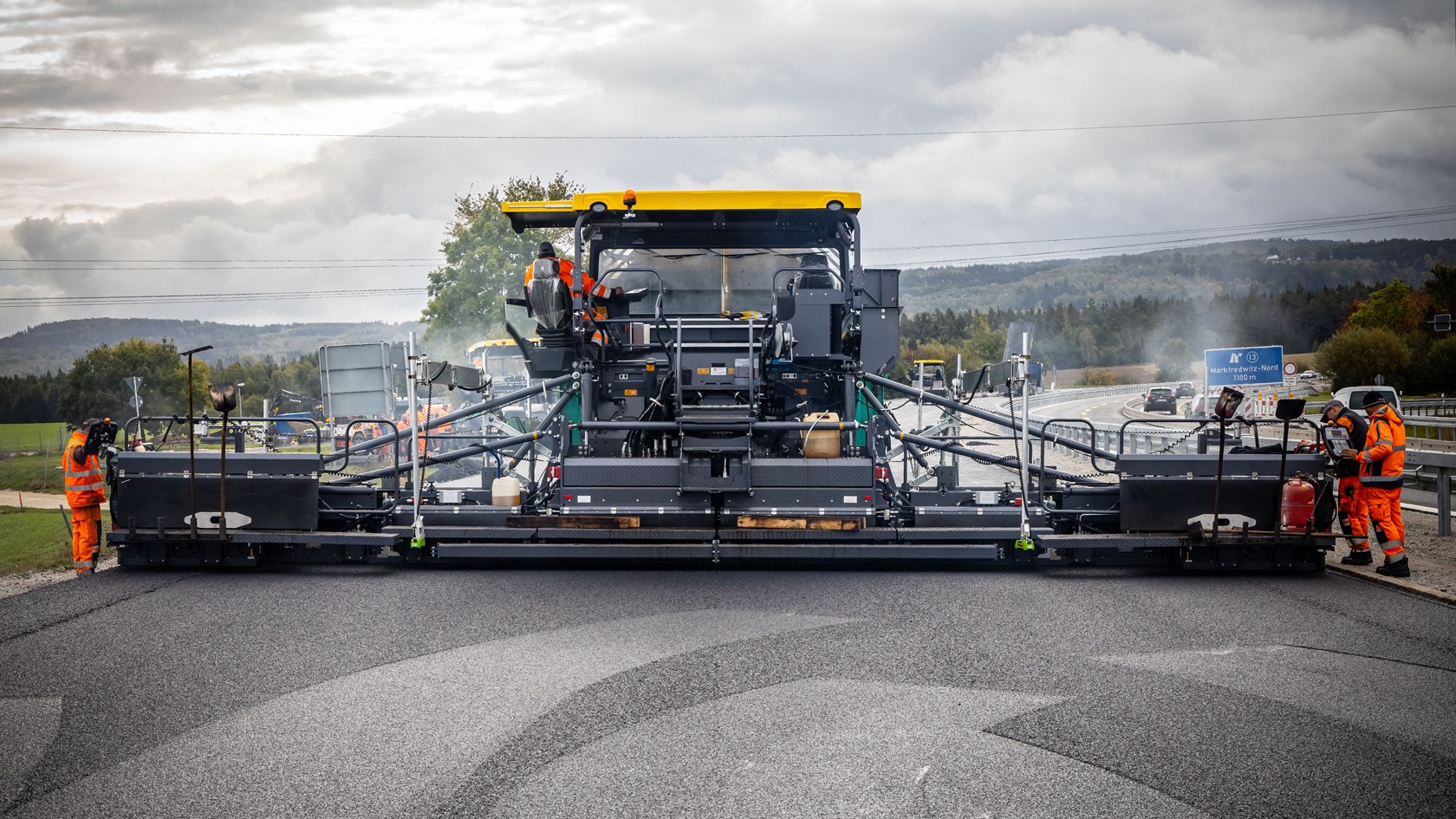
The paving screed is the heart of every road paver. The tasks of the screed in the paving process are as follows:
Generally speaking, there are two different screed types.
The operating principle behind all paving screeds
The screed components shown here all have a direct or indirect influence on paving quality.
(1) Torque restraint system
(2) Single-tube telescoping system
(3) Hydraulic cylinder for width adjustment
(4) Hydraulic screed extension
(5) Screed plate with heating rod
(6) Screed base member
(7) Heating rod monitoring system
(8) Eccentric vibration
(9) Tamper bar with heating rod
The metering gates push the material placed in front of the screed forwards. The tamper at the front end of the screed strikes off the mix as it passes under the screed to create the necessary precompaction and essentially determines the ‘floating behaviour’ of the paving screed.
The screed plates are responsible for ensuring the evenness of the pavement surface.
The pressure bars are pressurised by pulsed-flow hydraulics, and are the final components of the VÖGELE high compaction screeds.
These components enable the screed to deliver a perfect paving result with extremely high precompaction that reduces subsequent final compaction with rollers to a minimum.
All compaction aggregates are fitted with heating rods that prevent the adhesion of asphalt and ensure the production of a faultlessly sealed surface.
Together with the guide strips and sliding blocks, the telescoping tubes and the torque restraint system guarantee the necessary rigidity of the extending screed.