KLEEMANN Brechwerkzeuge für Prallbrecher
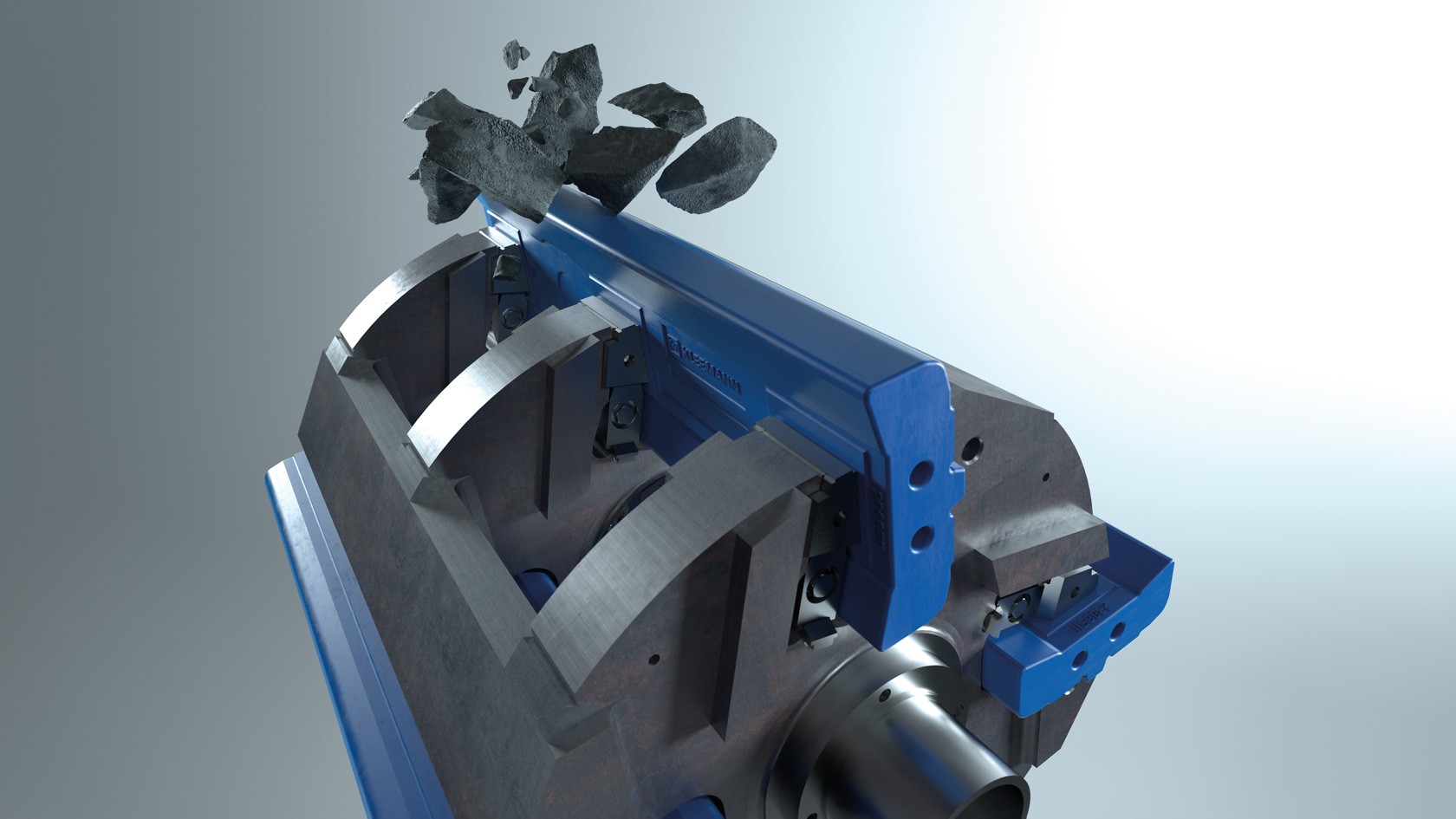
Die Einsatzbereiche eines KLEEMANN Prallbrechers sind vielfältig. Von der klassischen Natursteinverarbeitung über das Recycling von Baurestmassen bis hin zu Mining-Anwendungen stehen vor allem zwei Aufgaben im Fokus: Die Standzeit erhöhen und die Betriebskosten senken. Die Brechwerkzeuge unterliegen abhängig von verschiedenen Einflussfaktoren einem unterschiedlich starken Verschleiß.
Original KLEEMANN Schlagleisten bieten mehr als nur die richtigen Abmessungen. Die verwendeten Materialien, Legierungselemente und der gesamte Gussprozess sind wichtige Grundlagen für ein zuverlässiges Brechwerkzeug. Die Einsatzbereiche eines KLEEMANN Prallbrechers sind vielfältig. Von der klassischen Natursteinverarbeitung über das Recycling von Baurestmassen bis hin zu Mining-Anwendungen stehen vor allem zwei Aufgaben im Fokus: Die Standzeit der Schlagleiste erhöhen und Betriebskosten senken.
Der wirtschaftliche Einsatz der Schlagleisten wird durch viele Faktoren beeinflusst, z. B. Aufgabematerial, Rotordrehzahl, Feuchtigkeit, Aufgabegröße, Zerkleinerungsverhältnis. Ermitteln Sie mithilfe der folgenden Punkte die für Ihren Anwendungsfall optimale Schlagleiste. Gelangen Sie zu einer Auswahl von verschiedenen Schlagleisten, starten Sie Ihre Anwendung mit dem wirtschaftlich optimierten Brechwerkzeug.
Ausführung | Werkstoff | Kleemann Benennung | Eigenschaften | Empfohlene Anwendung |
---|---|---|---|---|
Monolithische Schlagleisten | Mangan Stahl | TRON.Mn | Manganstahl wird eingesetzt, wenn eine hohe Schlagbeständigkeit oder Dehnungsfähigkeit vorausgesetzt wird. Bei ausreichender Schlagkraft verfestigt sich der Manganstahl der Schlagleiste (Kaltverfestigung) und verringert somit den Verschleiß. | |
Martensitischer Stahl | TRON.M | Dieser Stahl vereint Härte und Schlagbeständigkeit, wenn der Einsatz von Chromstahl zu Bruchschäden führen würde. Des Weiteren haben martensitische Schlagleisten bei Anwendungen mit abrasiven Materialien eine längere Lebensdauer als Mangan-Schlagleisten. | ||
Chromstahl | TRON.C | Chromstahl zeichnet sich speziell durch seine hohe Härte aus und hat den Vorteil, besonders verschleißresistent zu sein, wo im Vergleich Manganstahl und martensitische Stähle schneller verschleißen. | ||
Metallmatrix-Verbundwerkstoffe | Martensitischer Stahl mit Keramikeinlage | TRON.MC | Die Schlagleiste besteht aus einem martensitischen Körper, der im Inneren mit Keramikeinlagen verstärkt ist. Dieser Verbundstoff kombiniert die Härte von Keramik mit den mechanischen Eigenschaften von Stahl und hat verglichen mit Schlagleisten aus Einzellegierungen eine 2–4mal so hohe Lebensdauer. | |
TRON.MC+ | Die Keramikeinlage ist tiefer und ausgedehnter eingegossen. Dadurch bleibt die Schlagkante bis zum restlosen Verschleiß erhalten. Dies bewirkt eine Erhöhung der Standzeit gegenüber herkömmlichen Martensit-Keramik-Schlagleisten bei abrasiveren Anwendungen. | |||
Chromstahl mit Keramikeinlage | TRON.CC | Der Verbund zwischen Chromkörper und Keramikeinlagen sorgt für ein gleichbleibendes Verschleißprofil bei sehr abrasiven vorgebrochenen Materialien, die speziell in Kiesgruben und Steinbrüchen vorkommen. |
Die richtige Beurteilung des Schlagleistenverschleißes ist die Voraussetzung für den wirtschaftlichen Betrieb einer Prallbrecheranlage. Ein Schlagleistenwechsel zum richtigen Zeitpunkt garantiert erfolgreiches Arbeiten und senkt erheblich die Betriebskosten. Die Schlagleisten verschleißen häufig nicht gleichmäßig über die gesamte Breite. Die Verschleißgrenze ist erreicht, wenn an einer Stelle der Schlagleiste das angegebene Mindestmaß erreicht ist.
Bitte beachten Sie, dass ein zu spätes Wechseln zu einem erhöhten Verschleiß am Rotor und der Schlagleistenbefestigung führt. Hierdurch entstehen teure Folgeschäden und lange Stillstandszeiten der Maschine. Neben einer erforderlichen Erneuerung der Rotorpanzerung (Hartauftragsschweißung) werden häufig auch die Klemmkeile für die Schlagleistenbefestigung beschädigt.