Genuine WIRTGEN
track pad systems
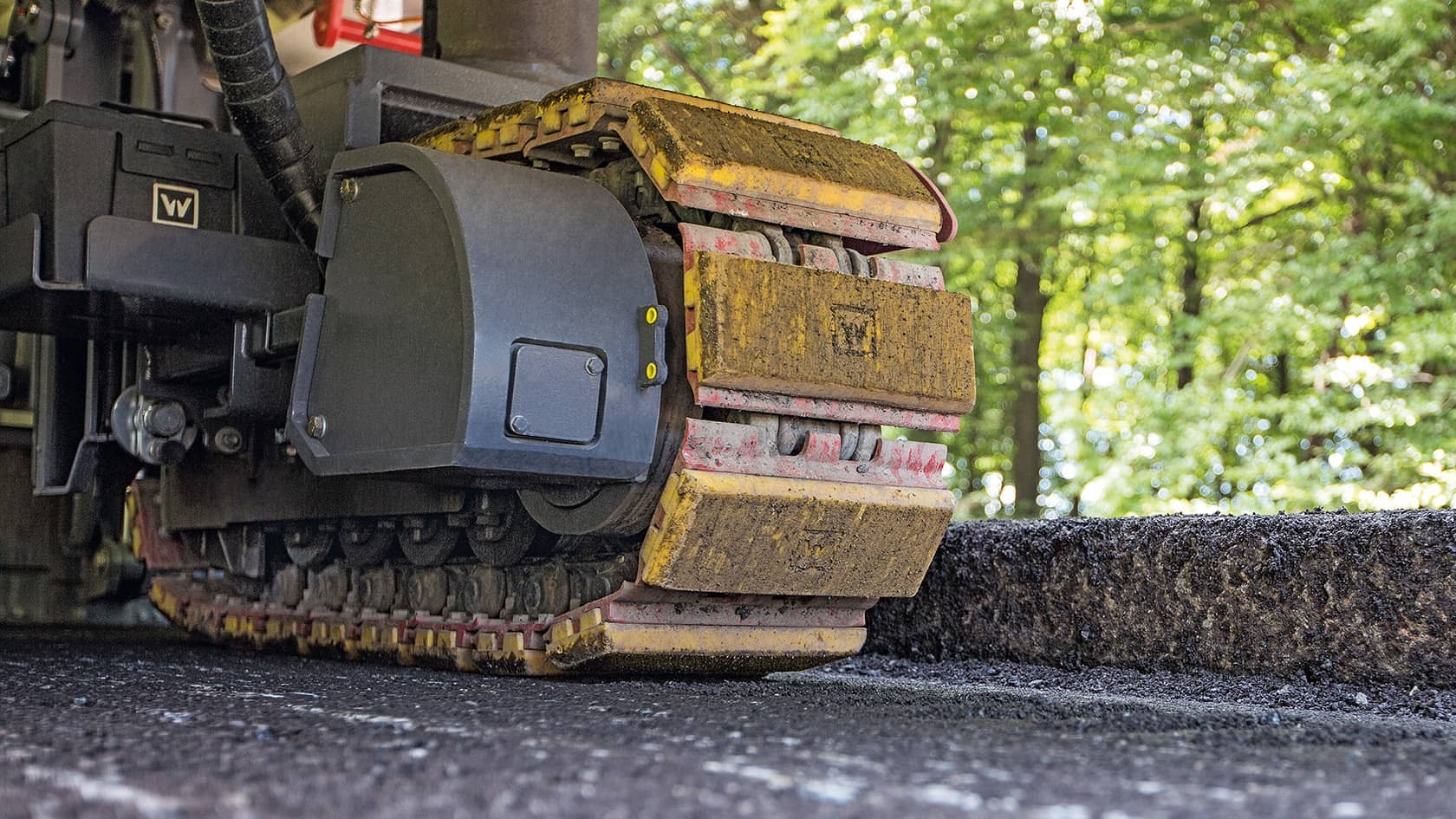
The term track pad include the base plate and the actual pad. The term base plate describes the steel plate that is connected to the track chain. The pads – polyurethane plates – are bolted to the base plates and ensure the necessary traction. The choice of track pads with respect to size and composition is primarily determined by the weight of the machine and the customer’s preferences.
Genuine WIRTGEN track pads are easy to recognise on account of their distinctive yellow and red colour combination.
The choice is yours!
WIRTGEN offers different base plate types to enable you, as our customer, to choose your preferred bolting method.
Regardless of your choice, all WIRTGEN track pads provide reliable traction on a wide variety of surfaces and also prevent possible damage to the asphalt pavement. You can never go wrong with genuine track pads from WIRTGEN.
Genuine WIRTGEN Poly Grip track pads consist of a tempered steel base plate manufactured from boron steel with a pad made from a polyurethane compound cast on top. The latter material was chosen due to the outstanding traction it provides on a wide variety of surfaces. Poly Grip track pads are mounted by direct attachment to the individual track chain links by means of nuts and bolts. The track pads impressively demonstrate their resistance to wear when, for example, machines are driven over sharp edges such as kerb stones or milled edges.
The logical further development of the genuine WIRTGEN track pad product family is the
Easy Pad System (EPS PLUS):
Replacement of track pads
As with all other nut and bolt connections, the track pad bolts/nuts must also be tightened with sufficiently high torque in the case of both the Poly Grip track pads and theEPS PLUS base plates from WIRTGEN. The following tables provide the correct tightening torque values for various WIRTGEN machines.
Machine model | Thread (mm) | Tightening torque | |
---|---|---|---|
Ma (Nm) | Ma (ft-lb) | ||
Bolts for Poly Grip track pads and EPS PLUS base plates from WIRTGEN |
|||
W 1000 F, W 1200 F, W 1300 F, W 100 F(i), W 120 F(i), W 130 F(i), W 100 CF(i), W 120 CF(i), W 130 CF(i), W 150(i), W 150 CF(i), W 1500, W 1900, W 195, W 200(F)(i), W 200 H(i) |
M 12 x 1 | 160 +/- 10 | 118 +/- 7 |
W 2000, W 205, W 215, W 210(F)(i), W 210 XP |
1/2“ UNF | 180 +/- 10 | 133 +/- 7 |
W 2100, W 220(F)(i) | 9/16“ UNF | 260 +/- 15 | 192 +/- 15 |
W 2200, W 250(F)(i) | 5/8“ UNF | 370 +/- 20 | 273 +/- 15 |
The use of EPS PLUS track pads on WIRTGEN machines enormously simplifies the work usually involved in fitting pads. Poly Grip track pads no longer have holes in which dirt can collect around the bolts, which previously made mounting a much more difficult task.
The most significant difference between the two systems (Poly Grip vs. EPS PLUS) is that, in the case of EPS PLUS, the steel base plates can remain on the track chain when worn track pads are removed. The steel base plates are attached in the same way as the Poly Grip track pads. Only the worn EPS PLUS polyurethane pad needs to be removed and replaced by a new one. When mounting WIRTGEN EPS PLUS track pads on their base plates, strict attention must also be paid to ensuring that the bolts are tightened with the prescribed torque in order to assure a secure connection between the pad and the steel base plate. The required tightening torque for the respective machines and crawler unit sizes can be found in the following table. Please also compare them with the latest values provided in the instruction manual. An adhesive locking compound on the special bolts prevents the pads working loose after tightening.
Please note: The bolts must be immediately tightened with the appropriate torque before the adhesive coating on the bolt thread hardens.
Machine model | Crawler size |
Thread size (mm) |
Tightening torque | |
---|---|---|---|---|
Ma (Nm) | Ma (ft-lb) | |||
Bolts for EPS PLUS pads from WIRTGEN | ||||
W 1000 F, W 1200 F, W 1300 F, W 100 F(i), W 120 F(i), W 130 F(i), W 100 CF(i), W 120 CF(i), W 130 CF(i), W 150(i), W 150 CF(i), W 1500, W 1900, W 195, W 200(i), W 200 H(i) |
W1 | M 12 x 1.5 | 150 | 110 |
W 2000, W 205, W 215, W 210(i) W 210 XP | W3 | |||
W 2100, W 220(i) | W4 | M 14 x 1.5 | 240 | 177 |
W 2200, W 250(i) | W5 |
Polyurethane track pads must be replaced when the wear limit of the pad is reached. Replacement should be carried out before the bars of the steel base plate become visible. The coefficients of friction (traction) of steel on asphalt are significantly worse than those of polyurethane or rubber. This has a direct influence on the possible advance speed and, consequently, on machine productivity. At the same time these coatings minimise damage to the ground and prevent possible payment of damages to the customer by service providers or owners of the construction machines. After all, roads or ground that were in good condition but were damaged due to worn track pads must, in general, be repaired or remade. If the steel bars of track pad become visible at the side, there is no reason to replace it.
The coating of the steel base plates (in the case of EPS PLUS track pads, the projection of the wider pads) serves to protect kerbs and other carriageway boundaries which could be damaged by contact with the steel of the base plate. The side layers of polyurethane pads may get torn when rolling over sharp edges or other obstacles, but this has no negative effects on the secure bond between the polyurethane and the steel base plate.