Wear check
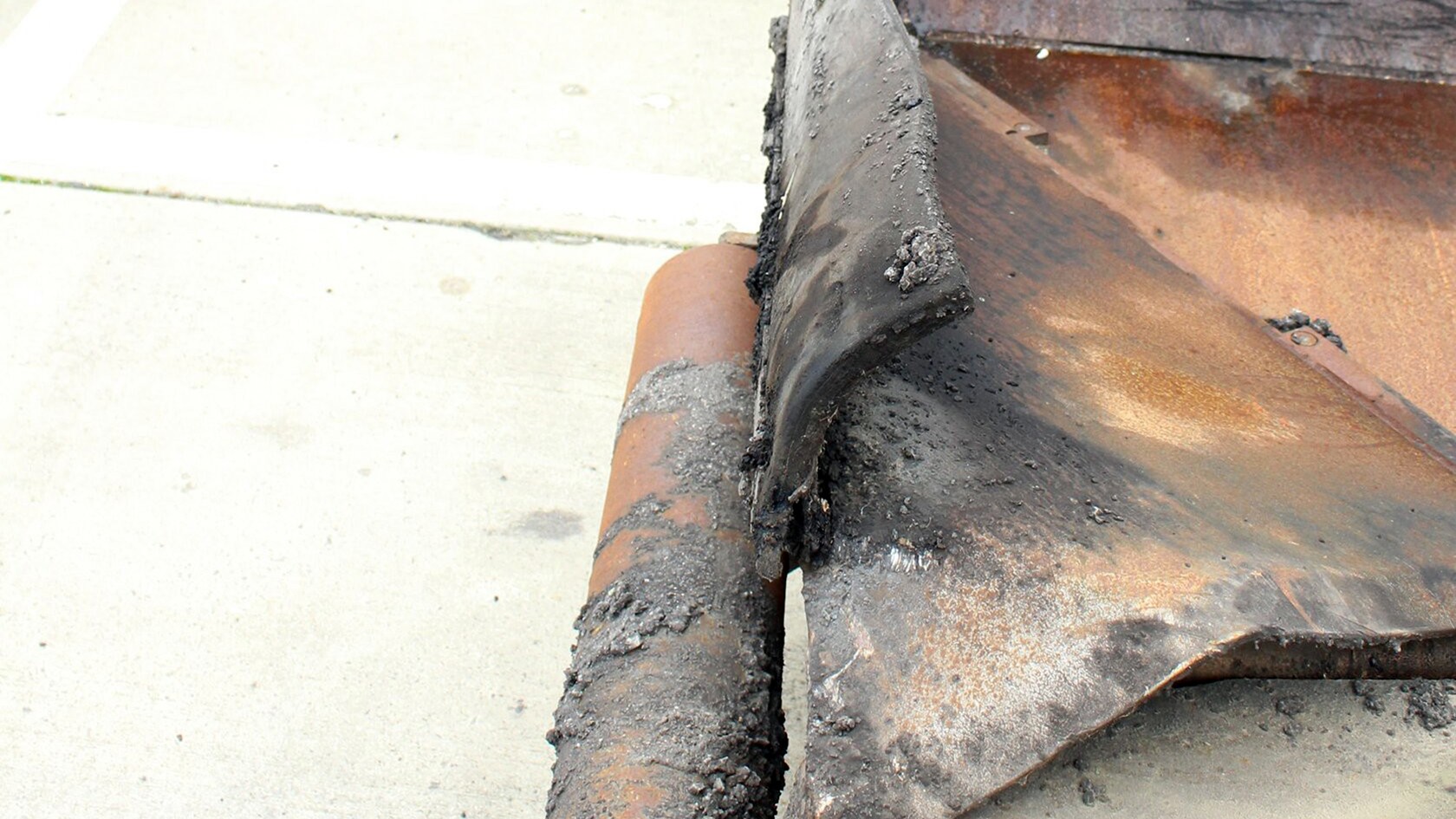
Wear is caused by the pressure between two elements in contact with one another (e.g. between the mix being paved and the conveyor) when these elements move relative to one another. In such cases, friction detaches small particles from the surfaces of both elements.
How can wear be avoided or prevented? Contamination with dirt increases wear: Abrasive materials grind material away at all points of contact and drastically shorten the service life of components. Regular maintenance and cleaning is essential for maximising the service life of components.
Extending service life means:
In the following, we tell you how to minimise wear and identify it in good time.
This could lead to loosening or detachment of the conveyor bars This would ultimately lead to an overall loss of mix conveying performance.