KLEEMANN Conveyor unit
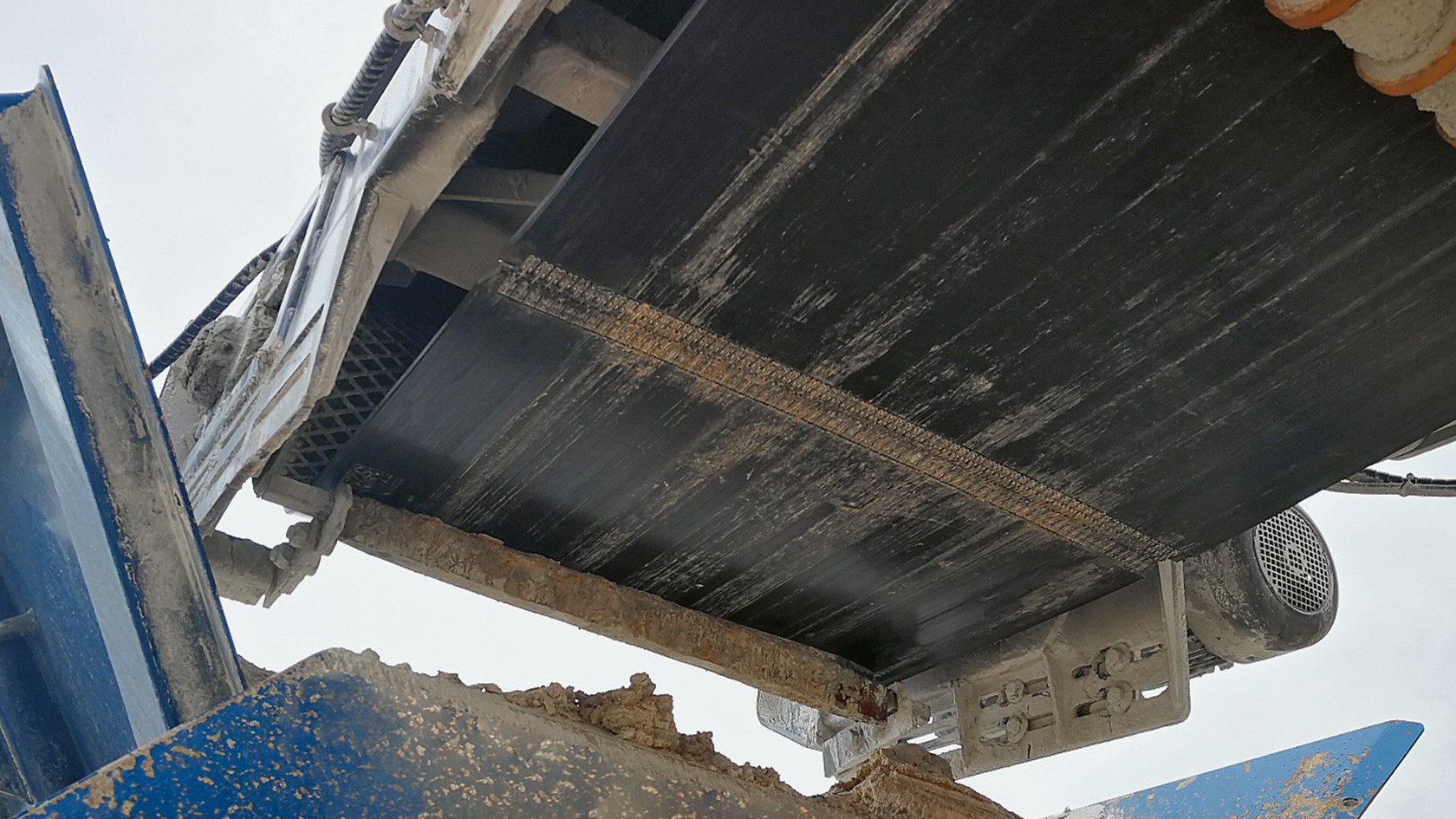
KLEEMANN offers conveyor belts for its crushing and screening plants in a variety of types and versions. Operators and users should select the options they need for their particular applications.
Conveyor belts are an elementary component of crushing and screening plants. Their performance strongly influences the overall performance of the plant. Due to their intended function, conveyor belts are constantly subjected to extreme stresses caused by the rock being conveyed. This is another reason why operators and users of KLEEMANN plants have such a wide range of types and versions to choose from. Whether endless, open or ZIP CLIP, with a smooth surface, a profiled surface, cleated or cleated with reinforcement – all KLEEMANN conveyor belts serve the same purpose: ensuring maximum productivity and plant utilisation rates.
Kleemann conveyor belts are constructed with multiple layers to cope with the extreme demands of materials processing. The topmost layer is designed as a large-dimensioned rubber cover plate. This is because the carrying side comes into direct contact with the material and is therefore subjected to particularly high wear.
Beneath this rubber cover plate, the belt is reinforced by woven fabric or steel cord inlays to ensure the necessary stability, impact-resistance and resistance to the tensile forces that are generated during use. An additional layer of rubber between the fabric inlays protects them against mechanical wear and the effects of chemicals on the conveyor belt. The bottom layer of the conveyor belt consists of a rubber plate on the running side. This ensures the smooth running of the belt on the support rollers.
Kleemann conveyor belts are fabricated in several layers. Their resilience is ensured by layers of solid rubber and inlaid, woven fabric reinforcement.
Kleemann offers three different conveyor belt systems that essentially differ in the ways they are assembled and disassembled All three systems are also available in a range of versions. Here, operators and users take the respective application into consideration and assure maximum productivity.
All three conveyor belt systems are available in a variety of types and versions, which allow plant operators and users to make exactly the right choice for their particular application and assure maximum productivity.
The costly and time-consuming replacement of defective or worn conveyor belts in crushing and screening plants is now a thing of the past. Thanks to ZIP CLIP replacement belts, belt changes can now be carried out quickly and efficiently. Once the belt is installed and tensioned, the machine is immediately ready to go again and work can continue.