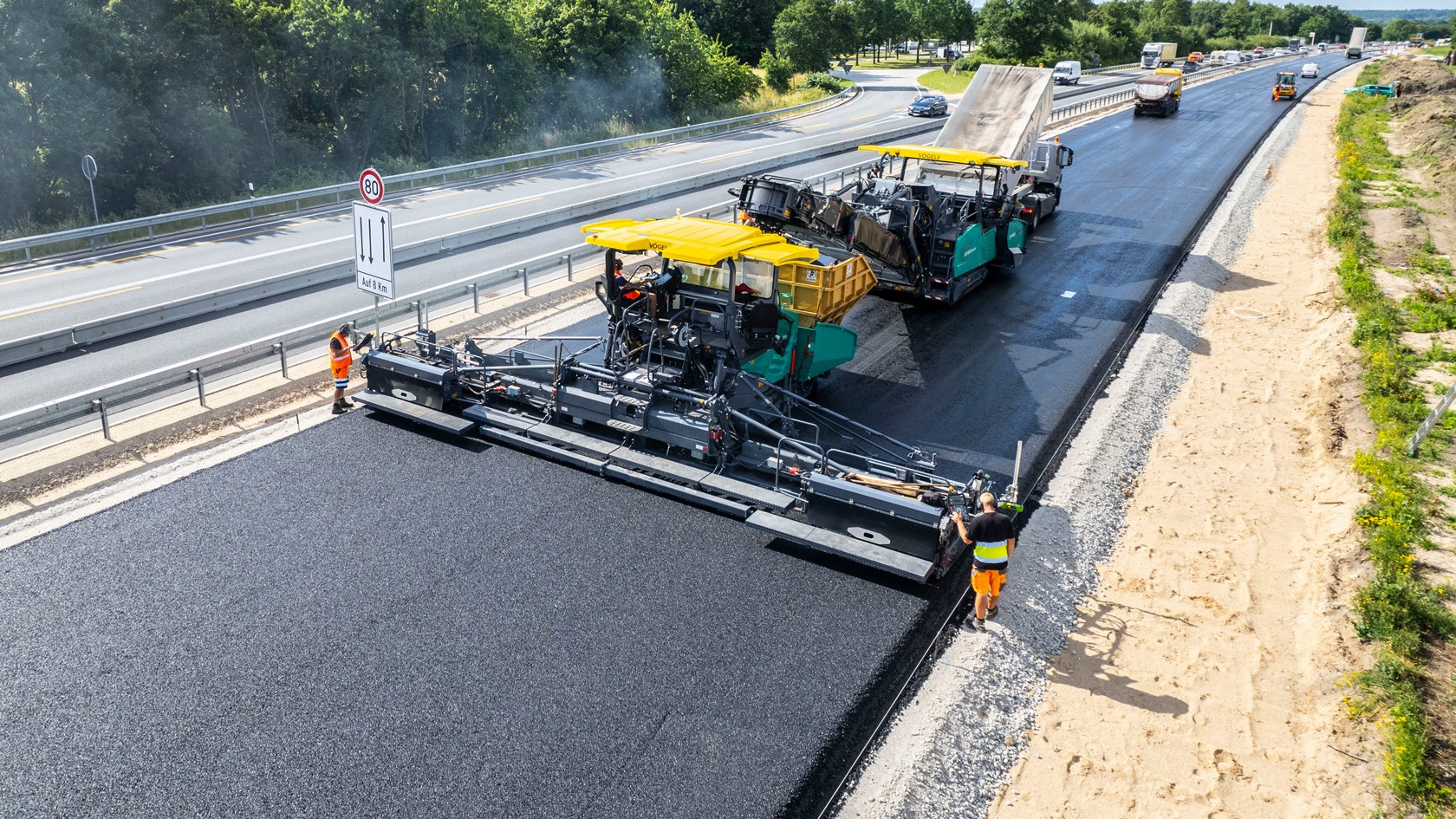
Die Verdichtungsaggregate der Bohle sollen eine möglichst große Vorverdichtung erzeugen, damit unterschiedliche Einbaustärken einen geringen Einfluss auf das Walzmaß bei der Endverdichtung haben. Bei VÖGELE kommen die im Folgenden aufgeführten Verdichtungsaggregate zum Einsatz:
Einsatzgebiete
V- und TV-Bohlen kommen bei allen üblichen, leichter zu verdichtenden Mischgütern zum Einsatz. Beim Einsatz von TP1- und TP2-Bohlen ist ein geringerer Aufwand bei der Nachverdichtung erforderlich. Die beiden Varianten unterscheiden sich hinsichtlich der zu erzeugenden Verdichtungswerte, wobei alle üblichen Mischgüter bearbeitet werden können. Die TP2-Ausführung liefert eine hohe Vorverdichtung gerade auch bei großen Einbaustärken.
TVP2-Bohlen können für alle üblichen Mischgüter verwendet werden. Darüber hinaus eignet sich diese Variante auch für den Einbau von PCC (Paver Compacted Concrete), da bei dieser Anwendung anschließend keine Nachverdichtung mehr erfolgt. Die Variante TP2 Plus mit nochmals gesteigerten Verdichtungswerten kommt im VÖGELE InLine Pave-Zug zur Erzeugung der Binderschicht zum Einsatz. Diese Schicht muss aufgrund des unmittelbaren Überfahrens des nachfolgenden Fertigers bereits Endverdichtungswerte aufweisen. Alle Verdichtungsaggregate bei VÖGELE Bohlen – Tamper, Vibration und Pressleiste – werden getrennt gesteuert und lassen sich nach Bedarf zu- oder abschalten.
Verdichtungsaggregate der Ausziehbohlen