KLEEMANN Screening
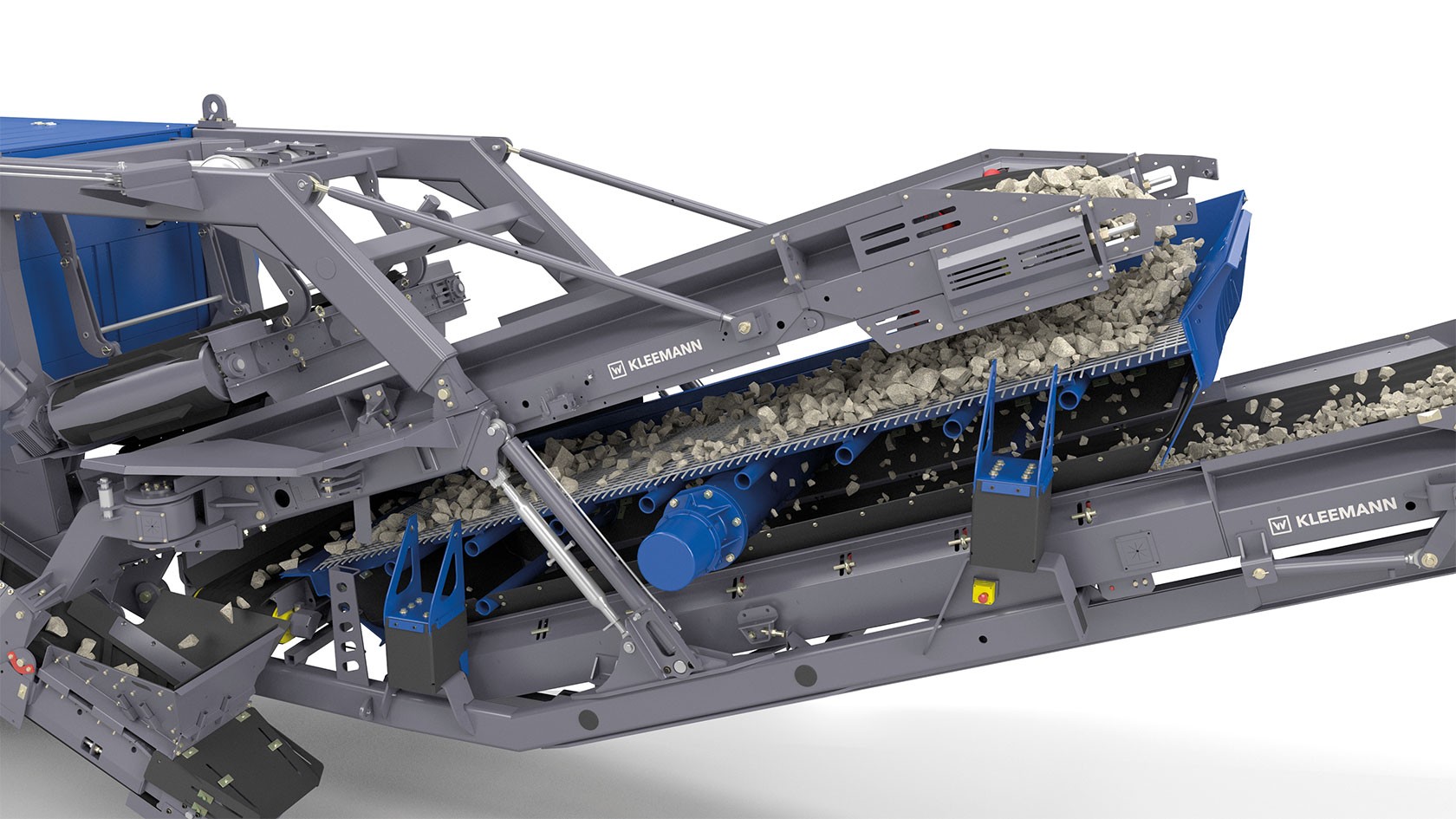
Screen media face tough challenges in the course of their daily work. In order to ensure constant and reliable screening of the desired material, genuine KLEEMANN screen media must fulfil particularly stringent quality requirements.
The screening result itself is determined by numerous factors. The most important of these are the shape of the particles, the moisture content and the feed volume. KLEEMANN offers a wide range of screen media for the upper and lower decks of screening plants that can be fitted to assure the best final screening results in any specific application. The individual screen segments can be freely configured in all cases. Flexibility is the name of the game – for every screening application.
Woven square mesh screens are made from wear-resistant and vibration-resistant spring steel wires. Special weaving techniques used in the production of the oscillating woven screens exploit the benefits of equal loading of the round wires at the intersections to achieve stable positioning of the wires and a regular mesh size.
Screen tensioning: Cross-tensioned and longitudinally-tensioned wires
W-HARPS are screens made from crimped, round cross-section longitudinal wires that run perpendicular to the screening plane and are interwoven with groups of three cross wires at certain intervals. The length of the slots is generally between 100 and 150 mm.
The consistent spacing of the cross wires ensures greater stability and better constancy of the mesh aperture than in the case of G-harps.
Screen tensioning: Longitudinally tensioned
G-HARPS are screens made from smooth and thin longitudinal wires that form slots. The large surface area of the screen enables high throughput of materials. The freely positionable and adjustable interwoven cross members ensure stable seating on the crossbeams of the screen box.
Screen tensioning: Longitudinally tensioned
S-HARPS are mesh-like screens made from round cross-section longitudinal wires with continuous crimping in the screening plane. The freedom of the individual longitudinal wires to move back and forth generates natural oscillations that make the screen ‘elastic’ and enables the processing of feed materials that are difficult to screen.
Screen tensioning: Longitudinally tensioned