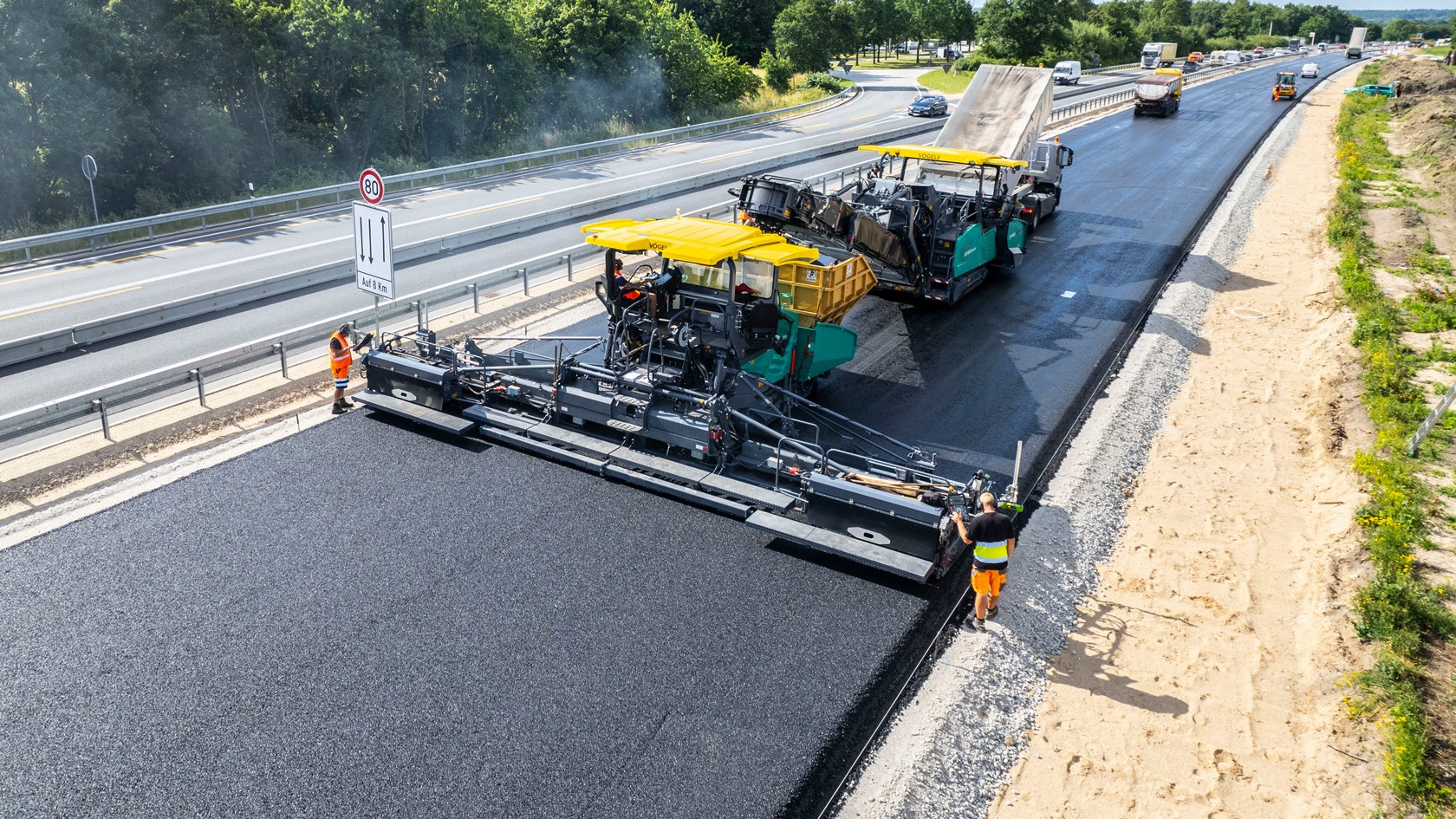
I gruppi di compattazione del banco dovrebbero realizzare la massima precompattazione possibile, in modo che i diversi spessori di stesa abbiano un impatto ridotto sulla massa di compattazione nella compattazione finale. Alla VÖGELE sono impiegati i gruppi di compattazione elencati di seguito:
Aree di impiego
I banchi V e TV sono impiegati con tutti i conglomerati comuni, semplici da compattare. In caso di impiego dei banchi TP1 e TP2 è necessario uno sforzo minore nella compattazione successiva. Le due varianti si differenziano rispetto ai valori di compattazione da produrre, mentre possono essere lavorati tutti i conglomerati più diffusi. La versione TP2 fornisce un’alta precompattazione anche in presenza di grandi spessori di stesa.
I banchi TVP2 possono essere usati per tutti i normali conglomerati. Questa variante è inoltre adatta anche per la stesa di PCC (Paver Compacted Concrete), in quanto in questa applicazione non avviene nessuna compattazione successiva dopo la stesa. La variante TP2 Plus con dei valori di compattazione ancora maggiori è impiegata nel treno VÖGELE InLine Pave per la produzione dello strato di collegamento. Questo strato deve presentare subito dei valori di compattazione finale, dovendo essere immediatamente percorso dalla finitrice che segue. Tutti i gruppi di compattazione dei banchi VÖGELE – tamper, vibrazione e barra di compattazione – sono comandati separatamente e possono essere attivati o disattivati in caso di necessità.
Gruppi di compattazione dei banchi estensibili